In the process of concrete mixing, cement silos, as important equipment for storing and supplying cement, have a wide variety of types and unique characteristics. This article will introduce several common cement silos, including their characteristics, advantages, and applicable scenarios, in order to better understand and choose the appropriate cement silo.
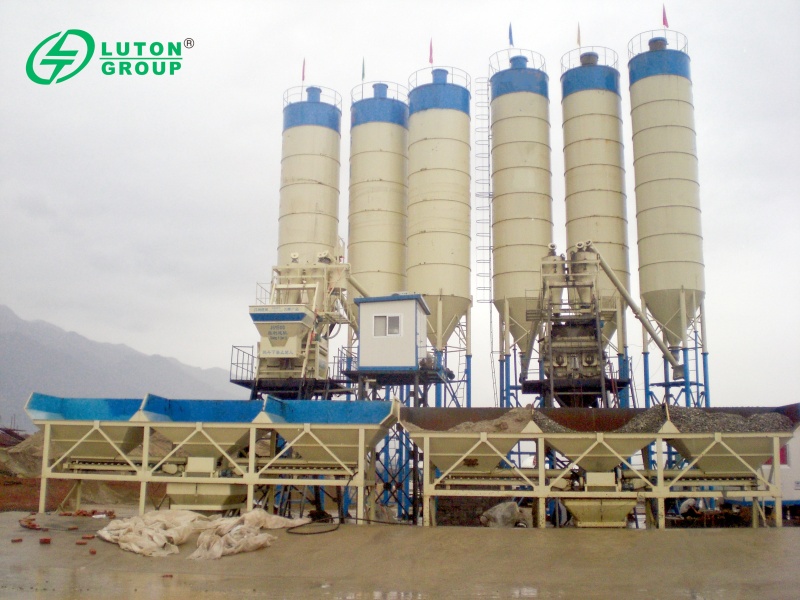
Steel Plate Cement Silos
Steel plate silo is a cement silo made by welding steel plates, which has high strength and durability. Its structure is sturdy and can withstand large pressures and impacts, making it suitable for large concrete mixing plants. The steel plate silo has a large capacity and can meet the demand for long-term and large-scale supply of cement. Meanwhile, the installation and maintenance of the steel plate warehouse are relatively simple and convenient to operate. However, the cost of steel plate silos is relatively high, and regular anti-corrosion treatment is required during use. Land on ltconcreteplant.com to get more details of concrete batching plants.
Galvanized Silos
Galvanized silo is a cement silo with a surface treated with galvanizing, which has good anti-corrosion performance. The galvanized layer can effectively resist oxidation and corrosion, extending the service life of the cement silo. Galvanized warehouses are usually used in outdoor environments and can withstand the effects of harsh weather. In addition, the appearance of the galvanized warehouse is beautiful and easy to clean. However, the cost of galvanized warehouses is relatively high, and in certain special environments, the galvanized layer may be damaged.
Canvas Silos
The canvas compartment is made of canvas material, which is lightweight and easy to fold. The canvas bin is suitable for temporary concrete mixing plants or mobile mixing equipment. Due to its simple structure, the cost of the canvas compartment is low, and it is easy to transport and install. However, the durability of the canvas compartment is relatively poor and is easily affected by weather and other factors, so it is necessary to pay attention to maintenance and replacement during use.
Plastic Silos
The plastic warehouse is made of high-strength plastic materials, which have good weather resistance and corrosion resistance. The weight of the plastic warehouse is light, making it easy to handle and install. Meanwhile, the cost of plastic silos is relatively low, making them suitable for small and medium-sized concrete mixing plants. However, the strength of plastic silos is relatively low and may not be able to withstand excessive pressure and impact.
In summary, various cement silos have different characteristics and advantages, and are suitable for different occasions. When selecting a cement silo, it is necessary to comprehensively consider factors such as the scale of the mixing plant, operating environment, and cost budget. Steel plate silos are suitable for large mixing plants and have high strength and durability; Galvanized warehouse is suitable for outdoor environments and has good anti-corrosion performance; The canvas bin is suitable for temporary or mobile mixing equipment, lightweight and easy to fold; Plastic silos are suitable for small and medium-sized mixing plants with lower costs. By selecting and using cement silos reasonably, the efficiency and quality of concrete mixing can be improved, production costs can be reduced, and sustainable development can be achieved.
There are various classifications of cement silos, which can be classified not only by material but also by appearance. Below, we will provide a detailed introduction to the characteristics, advantages, and usage scenarios of vertical and horizontal cement silos.
Vertical Cement Silo
Vertical cement silo is relative to horizontal cement silo and is usually used to store various bulk materials such as grain, cement, fly ash, etc. Its structural characteristics mainly include the warehouse body, ladder, guardrail, feeding pipe, dust collector, safety valve, high and low material level gauge, discharge valve, etc. These parts are welded with high-strength steel plates, so they have good sealing performance, can prevent moisture and insects, and keep the materials dry and loose.
The advantages of a vertical cement silo are its large capacity, flexible design, and the ability to customize according to customer needs. In addition, the new cement silo also focuses on green and environmentally friendly manufacturing, using environmentally friendly materials with minimal impact on the environment. Meanwhile, it has a long service life, good sealing performance, and can ensure material quality.
Vertical cement silos typically have high capacity and strong storage capacity due to their cylindrical or rectangular structure. Therefore, it is more suitable for storing large quantities of cement to meet the production needs of large concrete mixing plants. The height of a vertical cement silo is relatively high, usually around 8-15 meters, making it more suitable for use in situations with limited space, such as spacious construction sites or production workshops. In addition, vertical cement silos have less environmental pollution, are easy to operate, and can meet the actual needs of users. Therefore, it is usually used as a supporting product for large concrete mixing plants or construction sites.
However, vertical cement silos may face some limitations during transportation and installation due to their high height. For example, during transportation, height, width, and length may be restricted, leading to inconvenience in transportation. At the same time, before installation, it is necessary to prepare the foundation and ensure that it is firm before installation. If there are restrictions on the road conditions for entering the construction site, it may be necessary to carry out bulk welding to the construction site, which increases the complexity of installation. Therefore, in situations that require frequent movement or limited space, vertical cement silos may not be the best choice.
Vertical cement silos are suitable for large concrete mixing plants or situations that require a long and large supply of cement. Due to its large capacity and good sealing performance, it can ensure the continuity and stability of the concrete mixing process.
Horizontal Cement Silo
Horizontal cement silo is another common type of cement silo, with a lower vertical height and more cylindrical legs. The number of support legs varies depending on the type of horizontal cement silo. This type of equipment does not require a foundation, saving customers a lot of trouble.
The main components of a horizontal cement silo include feed conveying equipment, support legs, discharge cones, silo body, ladder, etc. Due to the fact that the gravity of its compartment can be dispersed, there is no need for a foundation or buried support, making installation convenient, time-saving, and labor-saving, as well as saving labor and costs. In addition, the horizontal cement silo has a lower height and a wider range of applications, making it particularly suitable for supporting equipment in indoor mixing plants or storing other powder materials, with less restriction on the roof. Meanwhile, due to its low height, it does not require external packaging and also saves usage costs.
However, the capacity of a horizontal cement silo may be relatively small and not suitable for situations that require a large amount of cement storage. Therefore, when choosing to use a horizontal cement silo, it is necessary to consider the actual demand and storage capacity.
The horizontal cement silo is a square or rectangular structure, supported by several legs at the bottom, and has a lower overall height, making it more suitable for mobile mixing plants or foundation free concrete mixing plants. Due to the design of the bottom support legs of the horizontal cement silo, it is easy to disassemble and assemble, and the transportation height and width do not exceed the limit. Ordinary trucks can be used for transportation on the road. Therefore, horizontal cement silos are suitable for situations that require frequent movement, such as temporary mixing plants or recycling between different construction sites.
In addition, the horizontal cement silo requires a higher volume requirement and a larger footprint, but its impact on cement quality is relatively small, with good safety and easy cleaning and maintenance. Therefore, it has advantages in high-capacity storage requirements, as well as in cement production plants, cement transfer stations, and other situations. However, due to the relatively small capacity of horizontal cement silos, they may not be suitable for situations that require a large amount of cement storage.
In summary, there are significant differences in the usage scenarios between vertical cement silos and horizontal cement silos. Vertical cement silos are suitable for large concrete mixing plants or situations with limited space, and have large capacity and strong storage capacity; Horizontal cement silos are more suitable for mobile mixing plants or situations that require frequent movement, with the characteristics of easy disassembly and transportation. When selecting a cement silo, comprehensive consideration should be given based on specific usage scenarios and needs.